Safety-Driven Lean Operations: Building Efficiency and Protecting Workers
Lean operations are widely applied across industries to reduce waste in areas like overproduction, waiting, transportation, inventory, motion, over-processing, and defects.
Tackling these inefficiencies in warehouse operations enables organizations to streamline workflows and enhance customer value. Embedding safety principles into lean practices further strengthens these efforts, supporting both productivity and employee well-being.
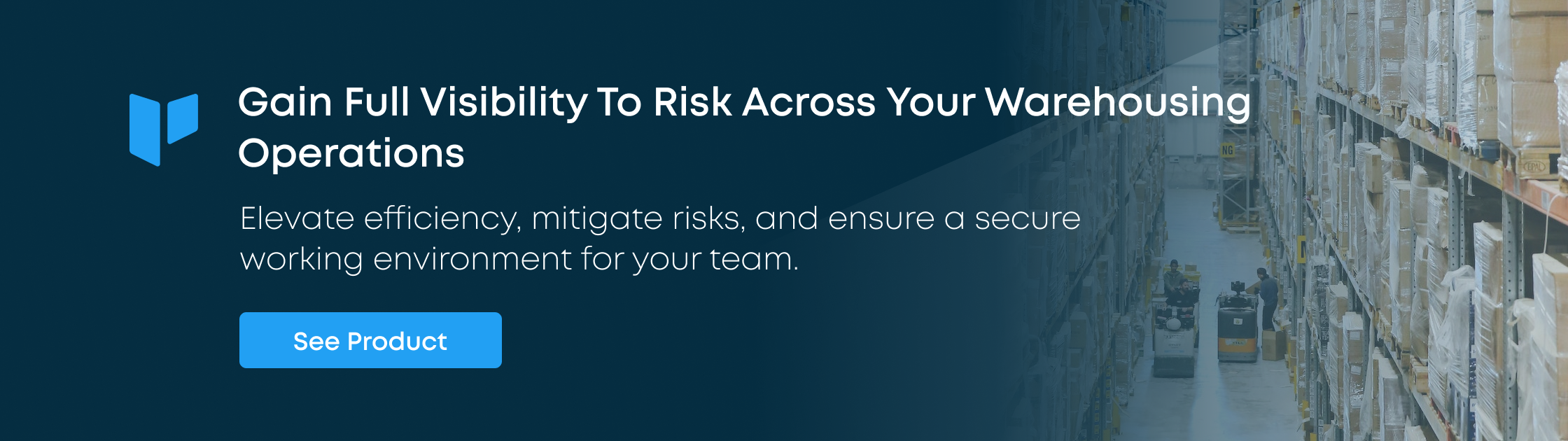
What are Safety-Driven Lean Operations in the Warehouse?
The logistics and supply chain sector, particularly warehousing, is characterized by complex operations, demanding schedules, and the consistent need for efficiency.
Integrating safety-driven lean strategies into warehousing creates an optimized approach that addresses both process streamlining and risk mitigation.
This integrated approach demands comprehensive training. Warehouse staff must understand lean methodologies and recognize their safety benefits.
Integrating Safety Drills with Lean Training
Merging safety drills and lean training sessions can lead to a more holistic understanding of how efficiency and safety coexist. One of the most impactful lean principles that can be integrated into warehousing operations is the Kanban system.
For instance, in a warehouse dealing with automotive parts, implementing a Kanban system prevents overstocking shelves. This ensures optimal quantity levels while reducing safety risks in the warehouse.
When items are carefully stocked and the warehouse staff knows their locations, organizations can significantly reduce risk in warehouse operations. Using AI technology can also further reduce risks.
What are the Benefits of Focusing on Safety-Driven Lean Operations?
Safety-driven lean operations combine safety and lean principles, providing numerous advantages to organizations.
At the heart of this integration lies the alignment of objectives—while lean methods seek to eliminate inefficiencies and wastes, safety measures aim to prevent hazards and potential harm.
Together, they lead to a holistic approach that maximizes both productivity and well-being.
Cost Efficiency Through Safety Measures
One of the primary advantages is significant cost efficiency and savings.
Ensuring a safe working environment reduces accidents, helping businesses avoid expensive medical expenses, legal complications, and potential compensations.
It also reduces the risk of delays, which leads to smoother operations and fewer disruptions.
Boosting Employee Engagement and Morale
Safety protocols also reduce interruptions, ensuring that operations run seamlessly and productive hours are not lost to unforeseen incidents. This focus on safety practices elevates employee morale and engagement.
When employees recognize that their safety is a top priority, they develop trust and loyalty toward the organization. Such an environment increases job satisfaction and encourages active participation.
Employees are more likely to offer valuable feedback, leading to continuous improvements in hazard identification, safety procedures, and operational protocols.
Ensuring Consistent Quality in Delivery
In terms of product and service delivery, the integration of AI in warehouse automation ensures consistent quality.
Lean principles and rigorous safety inspections lead to standardized processes, resulting in fewer errors and defects. This commitment to quality strengthens the brand's reputation and builds consumer and client trust.
A company that can guarantee the well-being of its stakeholders and deliver high-quality products or services consistently stands out in competitive markets.
Achieving Compliance and Industry Leadership
Adhering to safety-driven lean operations ensures compliance with industry standards and regulations.
Proactively meeting or even exceeding these standards helps companies avoid potential fines and penalties and also position themselves as industry leaders.
This proactive approach enhances their market image, further attracting top-tier talent and discerning customers.
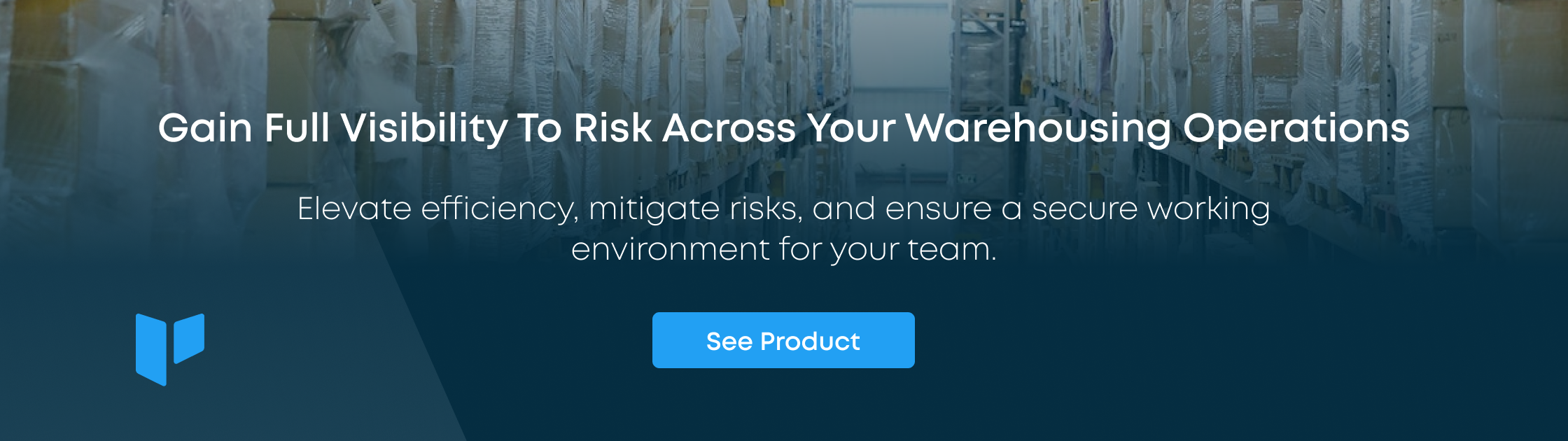
How to Implement Safety-Driven Lean Operations
Implementing safety-driven lean operations requires a strategic blend of lean practices and safety measures. This seamless union aims for operational efficiency without compromising the safety of employees and other stakeholders.
- Leadership Commitment
The first and foremost step is to secure the commitment of top management.
Leaders should emphasize the importance of safety-driven lean operations and advocate its principles.
Their buy-in is important as it sets the tone for the rest of the organization and ensures adequate resource allocation.
- Lean Process Mapping
Use lean tools like Value Stream Mapping to understand the existing workflow. Highlight areas of waste and inefficiency.
This analysis clarifies where safety and lean principles can intersect for maximum impact.
- Employee Training and Engagement
Equip employees with training sessions on lean methodologies and safety programs. Moreover, cultivate a culture of open communication where workers feel empowered to identify potential safety concerns or suggest improvements.
- Continuous Monitoring and Feedback
Establish regular checks and audits to uphold safety standards and ensure that lean operations evolve.
Feedback loops are essential to provide real-time insights into how the implemented strategies are performing and where adjustments are needed.
Remember that continuous workplace safety monitoring and improvements lead to enhanced safety performance over time.
Improve Productivity and Safety in the Workplace with Protex AI
Protex AI is an AI-powered workplace safety solution that integrates with your existing CCTV network.
It offers 24/7 seamless event capture, logging events, and creating reports that can help with safety audits.
These insights are vital for making data-informed decisions and shaping effective safety policies.
Check Out Our Industry
Leading Blog Content
EHSQ industry insights, 3rd Gen EHSQ AI-powered technology opinions & company updates.