Introductory Guide to Warehouse Safety in the Logistics and Supply Chain Industry
Warehouse safety is of paramount importance in the logistics and supply chain industry. Accidents in the warehouse can result in serious bodily harm and can also disrupt operations. As the backbone of global trade
How Can You Improve Warehouse Safety in the Logistics and Supply Chain Industry?
Warehouse safety in the logistics and supply chain industry is of paramount importance in the logistics and supply chain industry. Accidents in the warehouse can result in serious bodily harm and can also disrupt operations.
As the backbone of global trade and commerce, warehouses are often bustling hubs of activity where hazards lurk in every corner if not properly managed.
How to Improve Warehouse Safety
This guide aims to provide you with invaluable insights, practical solutions, and industry best practices to safeguard your most precious asset—your people—from potential accidents and injuries, while concurrently enhancing productivity and efficiency.
Through a deeper understanding of warehouse safety, we can transform these spaces into safer, more organized, and efficient work environments.
Why is Safety in a Warehouse Important?
The warehouse is one of the most important components of any business that involves physical products. It is where all products are stored before distribution, making it a crucial part of the supply chain.
However, warehouse environments are known to be dangerous due to the constant movement of heavy machinery, equipment, and people. Implementing effective logistics safety solutions is key to mitigating these risks.
Here are just a few reasons that outline the importance of warehouse safety.
Ensuring Employee Safety
One of the major reasons why warehouse safety is so important is because it improves accident prevention in the warehouse. Ensuring the safety of your employees is one of the most important things for warehouse managers. Taking proper steps to mitigate risks and hazards can go a long way in protecting your employees from serious harm.
Compliance with Regulations
Both the HSE and OSHA have a list of regulations that businesses must comply with. Businesses that fail to comply can face heavy fines and even lawsuits from injured employees.
Investing in safety measures to comply with OSHA regulations and warehouse health and safety requirements is not just about following rules - It shows that you value your employees' safety and take their well-being seriously.
The Cost of Accidents
An accident in a warehouse can bring your operations to a standstill and result in costly damages to products and equipment. Injured workers also mean missed time and lost production hours, which can hurt your bottom line.
Businesses with good safety records are also eligible for insurance discounts. With the high prevalence of workplace injuries in the warehousing industry, having a good safety record can save you thousands in premiums.
Boosts Morale and Productivity
Implementing and enforcing safety protocols can also improve employee morale and productivity. Employees who feel safe in their work environment are more likely to be productive.
A safer workplace also means fewer absences and lower turnover rates. Additionally, a safety-conscious workplace can lead to greater employee satisfaction and a positive company culture.
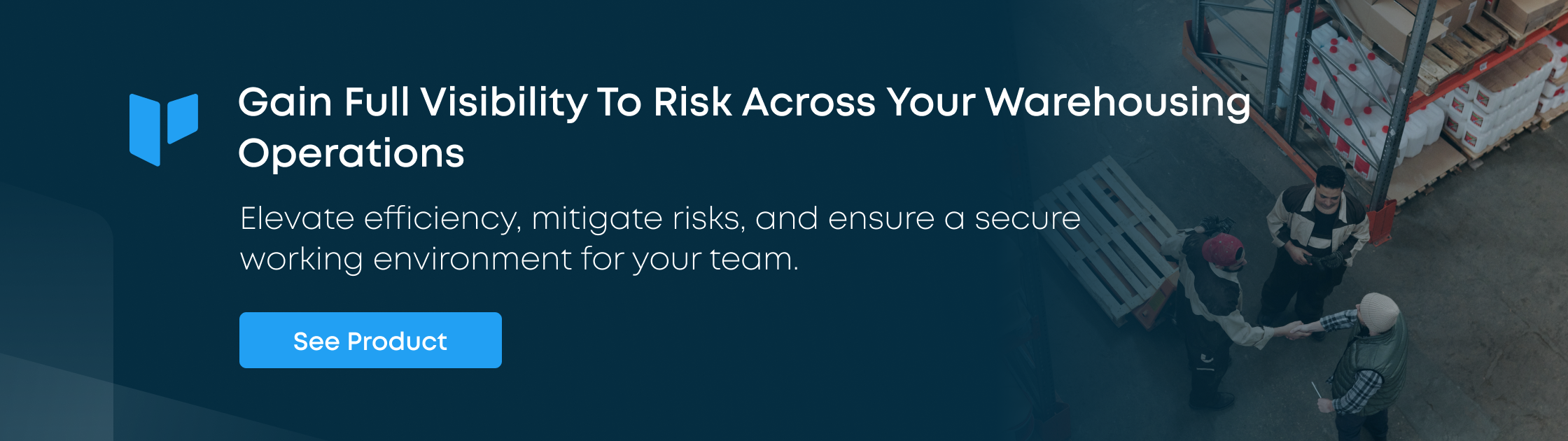
Warehouse Layout Optimization to Maximize Safety
Optimizing the floorplan layout of the warehouse is critically important for improving safety in the logistics industry. Companies can take a series of steps to improve overall safety by carefully reviewing the existing floorplan and analyzing operations.
This not only contributes to the efficiency of the operations but also ensures comprehensive supply chain safety by reducing the risk of accidents and injuries.
Strategic Traffic Flow Design for Warehouse Safety
Warehouse layout optimization is a critical aspect of safety management in logistics and supply chain operations. A well-planned layout not only maximizes operational efficiency but also significantly reduces the risk of accidents and injuries.
An optimally designed warehouse considers factors such as traffic flow, storage and handling of goods, positioning of equipment and workstations, and easy access to emergency exits. It begins with mapping the flow of goods and personnel, eliminating any cross paths that could lead to collisions or accidents.
Optimizing Aisle Widths and Pathways
Aisle widths should be designed considering the size and turning radius of the handling equipment. Clear and well-marked pathways help prevent incidents involving workers and moving equipment.
Safe Storage and Handling of Goods
Equally important is the strategic positioning of goods, placing high-volume items near the shipping area to minimize movement and potential mishaps.
Ensuring that hazardous materials are stored in designated areas with appropriate labeling and containment measures further reduces the risk of accidents and enhances overall logistics safety.
Preventing Falling Hazards with Proper Stacking
The stacking of goods requires special attention; improper stacking can lead to falling hazards. Using appropriate shelving and racking systems, with clear labeling and set weight limits, can go a long way in minimizing such risks.
Ergonomically Positioned Equipment and Workstations
Moreover, equipment and workstations should be positioned to promote ergonomics and ease of use, preventing strain-related injuries over time.
Incorporating ergonomic designs not only protects employees from repetitive stress injuries but also contributes to improved productivity and workplace health.
Emergency Exit Accessibility and Safety Equipment Placement
Emergency exits and safety equipment such as fire extinguishers and first-aid kits should be easily accessible, with clear signage guiding their location.
Regular drills and employee training on emergency response procedures ensure that everyone knows how to act quickly and safely in case of an incident.
Incorporating these safety measures in your warehouse layout optimization not only ensures compliance with safety regulations but also fosters a safety-conscious work culture that can significantly enhance productivity and morale.
Implementing Safety Awareness Programs in the Warehouse
Safety awareness programs play a key role in fostering a culture of safety within a warehouse environment. They are designed not only to educate workers about safety protocols but also to empower them to take responsibility for their own safety and the safety of their colleagues.
Effective implementation of such programs can significantly decrease the likelihood of accidents and near misses, enhancing overall warehouse productivity.
Conducting Hazard and Risk Assessments
Before implementing a safety awareness program, it's essential to carry out a comprehensive hazard and risk assessment of the warehouse. This helps identify potential dangers and provides the foundation for the program.
Tailoring Training Programs to Identified Hazards
Once the risks have been assessed, training programs should be developed, tailored to address these identified hazards. This might include training on safe use of machinery, lifting techniques, chemical handling, emergency procedures, and more.
Continuous Training and Regular Safety Meetings
Training should be continuous and not a one-off occurrence. Regular safety meetings can help refresh the team's memory of important safety protocols, and updates should be provided when there are changes to processes, equipment, or regulations.
Ensuring Accessible and Understandable Training
It's also essential that training is conducted in a language and format that all employees understand. A successful safety awareness program also encourages worker participation.
Encouraging Worker Participation and Feedback
Inviting workers to share their insights, experiences, and ideas can make them feel valued and heard. They can also identify safety hazards that might not be immediately apparent to management. Suggestions for improvement could be encouraged through an anonymous reporting system or suggestion boxes.
Recognizing and Rewarding Safe Behavior
An important aspect of any safety awareness program is recognizing and rewarding safe behavior.
This could be through a points system, where safe behavior earns points that could be redeemed for rewards, or through regular recognition of workers who uphold safety standards.
This not only motivates employees to follow safety protocols but also helps to build a positive safety culture within the organization.
If you're interested in how these technologies can revolutionize safety in your warehouse, our ultimate guide on AI safety warehouses provides comprehensive insights and practical applications that can help you enhance your safety protocols.
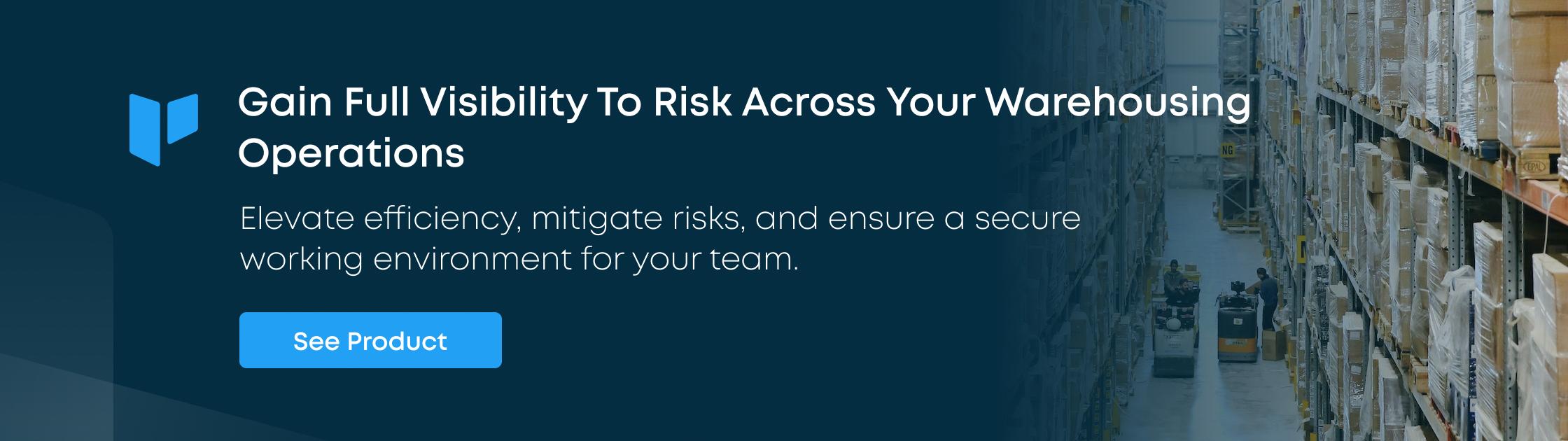
Safety Practices for Loading and Unloading
One of the first steps towards improving loading and unloading safety is effective planning and supervision.
Every task should be thoughtfully planned, considering the size and weight of goods, the equipment required, and the personnel involved.
A competent person should supervise the operations to make sure safety guidelines are followed consistently.
Appropriate Use of Personal Protective Equipment (PPE)
Workers involved in the loading and unloading process should always wear the necessary Personal Protective Equipment (PPE).
This may include safety helmets, high-visibility clothing, safety footwear, and gloves. PPE not only protects workers from potential harm but also enhances visibility, especially when working in areas with heavy machinery and vehicles.
Proper Equipment Operation and Maintenance
The use of appropriate and well-maintained equipment is crucial for safe loading and unloading. All equipment, including forklifts, pallet jacks, and hand trucks, should be regularly inspected and maintained.
Only trained and authorized personnel should operate these machines. This helps minimize equipment-related accidents and enhances operational efficiency within logistics operations.
Communication and Coordination
Clear communication and coordination among team members are essential during loading and unloading. When everyone is aware of their responsibilities and the tasks at hand, the likelihood of miscommunication and related accidents reduces.
Visual and audible signals, radios, and other communication devices can be effectively used to coordinate tasks, especially in noisy environments. This approach supports accident prevention in the workplace by ensuring that safety processes are consistently followed.
Major Risks Associated with Warehouse Safety
There are various risks associated with warehouse safety that must be kept in mind when designing processes. Effective warehouse hazard identification and adherence to warehouse safety procedures are key to mitigating these risks.
Slips, Trips, and Falls
Slips, trips, and falls constitute a significant proportion of warehouse injuries. These can result from wet or slippery floors, cluttered walkways, improper use of ladders, or poor lighting.
It's essential to keep warehouse floors clean and free of obstacles, ensure good lighting in all areas, and promote the correct use of equipment like ladders and safety harnesses for elevated work. Addressing these safety concerns promptly can minimize incidents almost immediately.
Forklift Accidents
Forklifts are essential in warehouse operations, but they can pose significant risks if not used correctly.
Accidents can occur due to overloading, improper training, mechanical faults, or careless operation. Implementing comprehensive forklift training, performing regular equipment inspections, and enforcing strict safety protocols can help mitigate these risks.
Manual Handling and Ergonomic Issues
Warehouses often require workers to lift, carry, push, or pull heavy objects, which can lead to musculoskeletal disorders. Additionally, repetitive tasks or working in awkward positions can contribute to ergonomic issues.
Training on proper lifting techniques, providing mechanical aids where necessary, and designing workstations ergonomically can help prevent these problems.
Fire and Explosion Hazards
Flammable materials, if not properly managed, can pose severe fire and explosion risks in a warehouse. This risk is exacerbated if the warehouse also stores hazardous substances.
Regular inspections, proper storage of flammable materials, suitable fire suppression systems, and clear emergency evacuation procedures are vital in mitigating these hazards.
Exposure to Hazardous Substances
Warehouses often store a variety of substances, some of which can be harmful to humans. Workers can be exposed to these hazardous substances through inhalation, skin contact, or accidental ingestion.
Proper storage, handling, and disposal procedures, along with suitable personal protective equipment (PPE), can protect workers from harmful exposure.
Incidents involving Falling Objects
Improper stacking of goods or failure of racking systems can lead to falling object incidents. These can cause serious injuries, especially if the objects are heavy or sharp.
Regular inspections of storage systems, proper training on stacking methods, and use of protective equipment such as safety helmets can reduce this risk significantly.
Warehouse safety procedure> should include comprehensive warehouse hazard identification techniques to prevent these incidents.
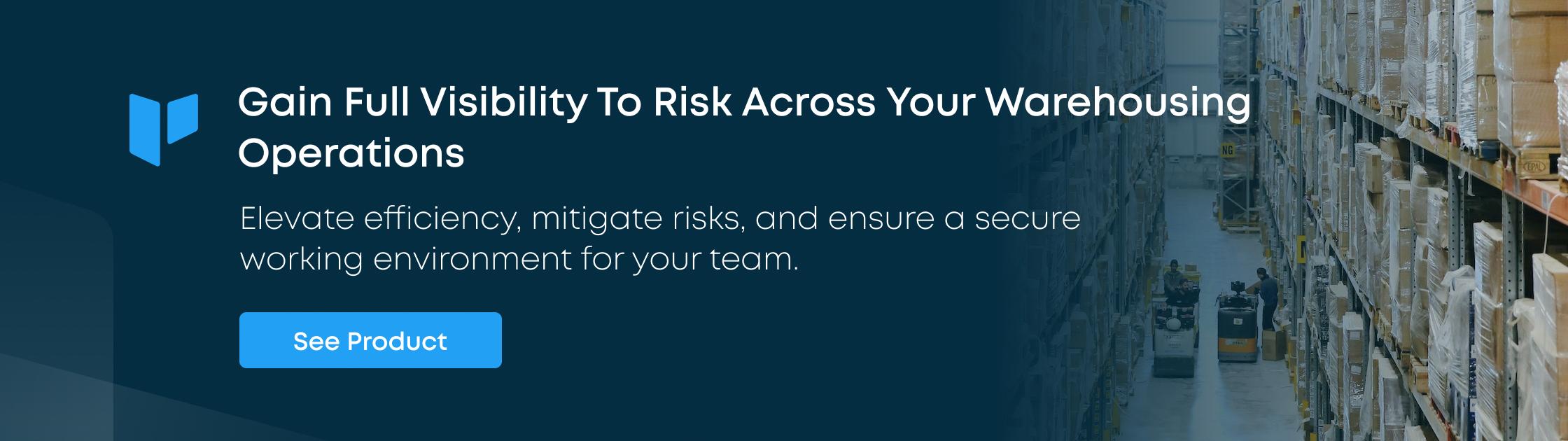
Important Regulations Associated with Warehouse Safety
In the United States, the Occupational Safety and Health Administration (OSHA) sets and enforces safety standards for the workplace. Some OSHA standards relevant to warehouse safety include:
- General Duty Clause: Employers are required to provide a workplace free from recognized hazards that are causing, or are likely to cause, death or serious physical harm to their employees.
- Material Handling (29 CFR 1910.176): This covers the safe handling and storage of materials, including secure storage of materials to prevent sliding or collapse, and clearances in loading docks.
- Powered Industrial Trucks (29 CFR 1910.178): This standard covers safety requirements for forklifts and other powered trucks.
- Walking-Working Surfaces (29 CFR 1910 Subpart D): These regulations cover safe working conditions to prevent slips, trips, and falls.
- Exit Routes (29 CFR 1910.36 and .37): These ensure that exit routes are clearly marked and unobstructed.
- Hazard Communication (29 CFR 1910.1200): This standard requires employers to inform and train employees about hazardous substances in the workplace.
European Union Regulations
In the European Union, the EU Framework Directive on Safety and Health at Work (Directive 89/391 EEC) obligates employers to implement necessary measures to protect the safety and health of workers. The directive has been transposed into various national laws among EU member states.
Health and Safety Executive (HSE) Regulations
In the UK, the Health and Safety Executive (HSE) sets and enforces safety standards. Some of their regulations relevant to warehouse safety include:
- The Health and Safety at Work etc. Act 1974:
This act places a duty on employers to ensure, as far as is reasonably practicable, the health, safety, and welfare at work of all their employees.
- The Management of Health and Safety at Work Regulations 1999:
This regulation requires employers to carry out risk assessments, make arrangements to implement necessary measures, appoint competent people, and arrange for appropriate information and training.
- The Manual Handling Operations Regulations 1992
These regulations apply to manual handling activities, requiring employers to reduce the risk of injury from those operations as far as reasonably practicable.
It's important for warehouse operators to familiarize themselves with the regulations that apply in their respective jurisdictions and to ensure they are fully compliant.
Environmental Health and Safety Considerations
Environmental health and safety (EHS) considerations play a critically important role in warehouse safety operations. The foundation of EHS practices lies in the identification and control of physical, chemical, and biological hazards.
Identifying and Controlling Workplace Hazards
From chemicals stored in the warehouse to the use of heavy machinery, each potential hazard must be meticulously identified and appropriate safety measures (including AI safety supply chain technologies) implemented. This includes providing suitable Personal Protective Equipment (PPE), implementing safe handling procedures, and ensuring proper ventilation.
Regular Risk Assessments and Safety Audits
Regular risk assessments and safety audits can further help in identifying new risks and evaluating the effectiveness of control measures. Incorporating predictive analytics into these audits can provide deeper insights, allowing for proactive adjustments to safety protocols before issues arise.
Effective Waste and Resource Management in Warehouses
Equally important is the management of environmental considerations within a warehouse.
This can include proper waste management procedures to prevent pollution, resource management initiatives to conserve water and energy, and the handling and storage of hazardous substances to prevent spills that could harm the environment.
Employee Training for Environmental and Safety Compliance
Employee training in these areas is crucial, as it ensures that everyone understands their role in maintaining a safe and environmentally friendly workplace.
Regular refresher courses and the integration of AI-driven monitoring systems can further reinforce these practices, helping to sustain long-term compliance and safety.
Ergonomics and Workspace Design for Employee Safety
EHS considerations also extend to ergonomic aspects. Implementing ergonomically sound practices can help minimize strain injuries and boost productivity.
This could involve designing workspaces that reduce the need for repetitive movements or heavy lifting, or providing equipment that helps employees perform their tasks more safely and efficiently.
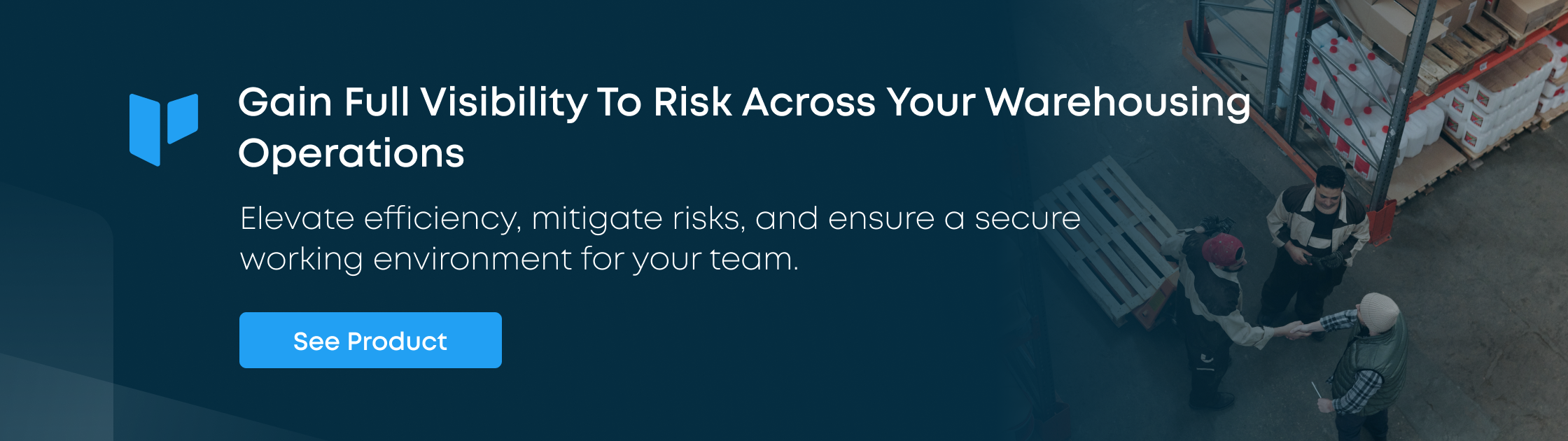
10 Tips for Creating a Safe Warehouse
If you want to create a safe warehouse, here are 12 tips that you should follow:
- Appropriate PPE
Making sure every employee has appropriate PPE is very important for creating a safe warehouse. This includes safety goggles, hard hats, and high-visibility vests. Recognizing how PPE enhances warehouse safety is vital for injury prevention and promoting a culture of workplace safety.
- Install Fall Protection
If you have multi-floor shelves in the warehouse, installing floor protection is very important. The use of harnesses and safety nets can go a long way in protecting employees from sustaining injuries, making them a necessary investment for effective warehouse safety management
- Comply with Rack Capacities and Measurements
There have been many cases where warehouse injuries have occurred because workers did not comply with max rack capacities and the measurements.
- Regularly Inspect Pallets
Pallets wear out over time and need to be replaced. Inspecting the pallets regularly can help reduce unsavory incidents. If you notice deck boards missing, a simple repair job can give them new life. This proactive approach is central to robust risk management strategies.
- Install Netting
Netting safety systems have been proven to reduce injuries and prevent objects from falling from the sides of a shelf, which can lead to severe injuries.
- Proper Illumination
Warehouses should be adequately lit. Because these are large spaces with shelves that go all the way to the ceiling, it’s imperative that there’s proper illumination throughout the building.
- Install Appropriate Signage
Making sure there’s appropriate signage throughout the warehouse is very important. Proper signage reinforces your safety procedures across the logistics sector. You need signs for compliance, danger warnings, hazard indications, and materials handling for maximum safety.
- Install Mirrors at the Corners
Having mirrors at the corners in longer aisles can help prevent safety accidents, especially with forklifts. Mirrors offer greater visibility and alert people about what’s around the corner.
- Regularly Inspect Fire Safety Systems
Making sure that fire safety systems are inspected at regular intervals and checked by professionals is a vital step towards warehouse safety. This step is critical not only for maintaining safety but also for effective incident reporting.
- Using AI to Improve Safety in the Warehouse
AI in the warehouse is a game-changer for worker safety. AI-based monitoring systems like Protex utilize machine learning and PPE detection using computer vision to identify potential hazards, including elements that might be overlooked by a safety inspector, such as a liquid spill or an improperly stacked item.
It can then alert warehouse managers or operators immediately, allowing them to take corrective action and prevent accidents. Moreover, Protex AI can identify and track unauthorized individuals, ensuring only authorized personnel access potentially hazardous areas.
This technology doesn't just improve employee safety monitoring - it sets a new standard for safety in the logistics industry.
AI-Driven Safety Monitoring and Exclusion Zones
The use of predictive analytics and security measures makes it easy for companies to roll out new rules and to ensure that worker safety is prioritized above all else.
For instance, using AI-based monitoring tools, companies can define exclusion zones and ensure hard hat detection is always in place.
These are areas where workers are not allowed due to safety reasons. This can be critically important in high-risk areas such as construction sites.
Regularly Revisit Your Warehouse Safety Plans
Conditions in warehouses change regularly. It’s important for warehouse safety managers to regularly revisit their safety plans and make amendments if need be.
The use of AI technology in the warehouse can help employees gain important insights about overall safety conditions and the most common areas where injuries occur.
With a tool like Protex AI, companies can ensure the safety of their workers and take proactive safety decisions without requiring safety officers on the scene all the time.
Protex AI plugs into the company’s existing CCTV network, and can be used for capturing unsafe events and for detecting any anomalies. These can prove to be vital when making important safety decisions for the warehouse.
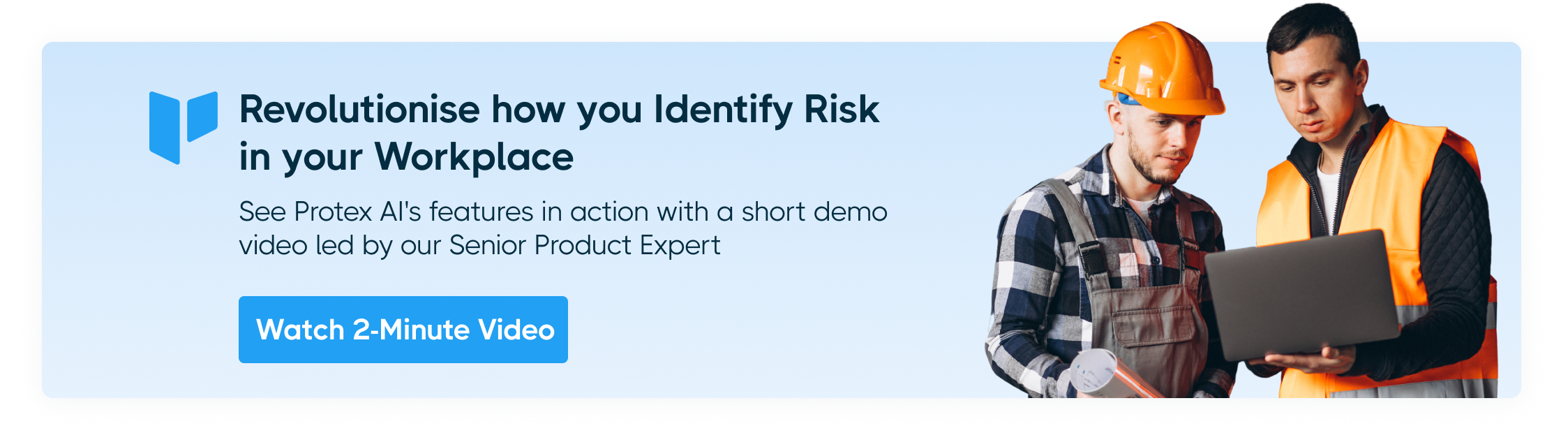