Near Miss Prevention: How Can Workplace Hazards Be Avoided?
Near misses and hazards can cause severe damage to people, processes, and the environment. They can lead to costly workplace injuries or illnesses, product or property damage, or financial losses.
While you cannot eliminate all risks in the workplace, you can take proactive steps to identify potential near misses and hazards, mitigate them before they become a problem, and avoid them entirely.
Avoiding Near Misses Through Proactive Safety Measures
It’s important for companies to take a proactive approach to workplace safety, and this is only possible when every stakeholder, from the management to the employees, understands the risks.
The terminology for near misses in the workplace or hazards is often company-specific, with some companies often using them interchangeably. However, both are quite different, as we’ll discuss below.
In this guide, we’re going to talk about practical steps that organizations can take to avoid near misses and hazards, and create a safer workplace. But first, it’s important to understand what near misses and hazards are, and categorize them accordingly.
What is a Near Miss in the Workplace?
Near misses can be defined as "incidents that had the potential to cause harm, but did not due to chance or preventive measures taken."
In essence, a near miss event is one that nearly caused harm but didn’t result in any injuries or damages. This can include anything from someone barely avoiding a slip-and-fall hazard to narrowly avoiding a collision with another vehicle on the highway.
Even though there were no immediate consequences of these events, they still indicate potential workplace hazards that should be addressed in order to prevent future incidents and injuries.
Call it a close call or a lucky escape, it’s important for EHS teams to understand why near misses must be reported, and what benefits they can get from identifying them.
Do Near Misses Prevent Future Incidents?
Near misses are valuable because they help identify potential hazards before they become a serious issue. By tracking these incidents, you can identify patterns in the workplace that could lead to future accidents or injuries.
For example, if you notice a pattern of near miss incidents involving a particular piece of machinery, you can take steps to fix the problem before someone gets hurt.
However, the problem usually arises when there’s no defined system in place for near miss reporting. This is mostly due to the safety culture in the organization, as a company may not treat a near miss seriously because no harm was done.
And yet, investigating near misses can prove to be valuable indicators of what can go wrong. By analyzing near misses, you can better understand what went wrong so you can develop strategies and solutions to prevent similar incidents from occurring again in the future.
Additionally, by proactively identifying and addressing potential risks before they cause harm, you can save your company time and money down the line.
Common Examples of Near Misses
Near miss examples can occur anywhere in the workplace - from the production floor to office spaces. Here are some common examples of near misses in the workplace:
- An employee trips over a loose wire but catches themselves before falling.
- A machine jams and stops running just before it could have caused serious harm.
- An employee almost hits their head on an overhead beam but ducks just in time.
- A piece of heavy equipment malfunctions but does not cause any injury or damage.
There are countless other examples of near misses that could occur in different workplaces. The key is to be aware of potential risks and take steps to prevent them from becoming actual incidents.
Why Are Near Misses Important?
Some might argue that near misses are actually more important than actual accidents because they provide insight into what may be wrong with current safety systems or procedures and can help with accident prevention by identifying potential risks before they lead to serious injury.
That's why it's so important for EHS teams to pay attention to them and take the appropriate action(s). By understanding the root causes of near misses, EHS teams can identify trends and address them before they become bigger problems.
For example, if workers are constantly forgetting their safety glasses when entering a specific area of the workplace, an EHS team would want to investigate this further by looking at things such as worker training, safety compliance, or policy enforcement in that area of the workplace.
This process is called Root Cause Analysis (RCA) and helps identify possible solutions to eliminate any risks associated with similar types of near-miss incidents in the future.
What are Workplace Hazards?
A hazard is defined as something that can cause harm or damage, either directly or indirectly. In the context of occupational safety and health, these hazards can be broken down into several categories, including physical, psychosocial, chemical, or ergonomic hazards.
Physical hazards include things like noise, radiation, extreme temperatures, sharp objects, and slippery surfaces. Chemical hazards include things like flammable liquids, asbestos particles, toxic fumes and dusts, solvents, and combustible dusts.
The term 'hazard' is often used interchangeably with 'risk', but there is an important distinction between the two. Risk assessment refers to both the probability and severity of harm or injury caused by a hazard, while a hazard itself is simply something that has the potential to cause harm or injury without considering its likelihood or severity.
The 3 Most Common Types of Workplace Hazards
While there are many types of hazards (generally depending on the nature of work involved), most can be grouped into the following categories:
- Physical Hazards
Physical hazards include anything that could potentially cause physical harm to an employee, such as heavy machinery, electrical equipment, toxic substances, heights, confined spaces, noise levels, and extreme temperatures.
It’s important for employers to identify potential physical hazards in their workplaces and create safety protocols to prevent employees from coming into contact with them.
This includes providing adequate protective gear when necessary such as gloves or face shields. Additionally, employers should provide training on how to safely use dangerous equipment and handle hazardous materials.
Following OSHA guidelines and collaborating with the National Safety Council can also support effective incident prevention strategies.
- Ergonomic Hazards
Ergonomic hazards refer to any type of risk associated with body posture or repetitive motion that can lead to musculoskeletal disorders (MSDs).
Common ergonomic risks include poor lighting, uncomfortable furniture or tools, repetitive motions (such as typing), lifting heavy objects without assistance from colleagues or machines, and sitting for long periods of time without breaks.
To reduce these risks employers should:
- Provide ergonomic assessments for new hires as well as regular assessments for existing staff members.
- Implement ergonomically-friendly workstations such as adjustable chairs or standing desks which give employees the option to stand while they work if they wish.
- Encourage regular breaks throughout the day so that employees don't stay in one position for too long at a time.
- Psychological Hazards
Psychological hazards have become increasingly common in today’s modern workplace due to longer hours and more stressful situations.
These types of hazards refer to anything that negatively impacts an employee’s mental health, such as:
- Bullying from fellow coworkers or supervisors
- Unhealthy work/life balance
- Difficult deadlines
- Excessive workloads
- Lack of feedback
- Job insecurity
To help mitigate these risks, employers should ensure their policies are up-to-date on issues like bullying or harassment and make sure they are enforced consistently throughout the organization.
Employers should also create anonymous feedback systems where employees can share their experiences honestly without fear of retribution so that problems can be addressed quickly before they escalate out of control.
Implementing a structured incident reporting system can help ensure that all workplace incidents are documented and addressed promptly.
How to Prevent Near Misses and Hazards in the Workplace
Now that you have a strong understanding of near misses and hazards, here are some simple strategies that you can use to prevent them in the workplace.
- Create a Positive Environment to Encourage Reporting
The first step is to create an environment where employees feel comfortable reporting potential risks or near misses - even if those risks don’t lead to actual incidents. This involves:
- Setting up systems such as anonymous reporting mechanisms so employees don’t feel like they need to keep quiet about potential hazards out of fear of retribution or punishment.
- Ensuring all employees receive adequate training to know how and when to report potential hazards or near misses.
- Regularly reviewing reports and keeping track of trends so that your team can address underlying issues before they become bigger problems down the line.
- Carry Out Thorough Investigations
EHS teams should also utilize proper investigative techniques when looking into near miss incident reports, such as conducting a root cause analysis (RCA).
RCA involves digging deeper into the incident to uncover any underlying factors that led up to it—like organizational structure, communication breakdowns, inadequate training, etc.—and then developing solutions based on those findings.
Not only does RCA help organizations effectively address safety issues before they become more serious problems; it also provides accurate data on which interventions will be most successful at preventing similar incidents in the future. It’s an essential part of any effective incident management and workplace safety program.
Whenever a near miss occurs, it’s imperative for EHS teams to conduct a root cause analysis and figure out what went wrong, and how such events can be avoided in the future.
- Develop a Hazard Identification and Management System
A hazard management system is a comprehensive process used to identify, assess, control, monitor, and review hazards that pose a risk in the workplace.
This should include hazard analysis that looks for any potential risk factors and assessing the likelihood of them occurring, controlling the risks with measures such as implementing safety precautions or training staff, monitoring the effectiveness of these controls, and regularly reviewing them to ensure they are up to date.
By doing this, you can dramatically reduce any potential hazards or near misses that could occur in your workplace. Using a workplace safety solution such as Protex AI can help businesses identify potential hazards before they occur, allowing companies to quickly detect potential hazards and take steps to mitigate the risks.
Protex AI allows organizations to leverage AI hazard detection to capture unsafe events in the workplace, empowering EHS teams by giving them access to crucial data when creating safety plans and taking important safety decisions.
- Regularly Conduct Safety Training Programs
Developing safety training programs for employees is critical as it helps ensure they understand how to properly use equipment, how to identify and analyze hazards in their environment, what steps need to be taken if an accident or incident occurs, and more.
Safety training programs should also include regular refresher courses so everyone remains aware of all applicable safety policies and procedures. This will help avoid any misunderstandings or mistakes that could lead to a hazard or near miss situation.
- Encourage Employee Engagement
Employee engagement is key when it comes to preventing near misses and hazards in your work environment. Employees should be encouraged to actively participate in discussions about safety regulations at team meetings or other gatherings where feedback can be discussed openly.
Employees should also feel empowered to raise any safety concerns they have without fear of retribution from their supervisors or colleagues – this will foster an open discussion that encourages collaboration between all parties involved which ultimately reduces the risk of any hazardous incidents occurring due to employee negligence or misunderstanding.
Use Protex AI to Improve Workplace Safety
Protex AI is an advanced monitoring solution that plugs into your company’s existing CCTV infrastructure. It uses AI safety software to automatically detect near misses or unsafe events, allowing EHS teams access to use crucial video evidence when making safety decisions.
It can be an invaluable tool for EHS managers and teams, giving them access to evidence that they can use to identify and address extreme hazards in the workplace, all without requiring constant supervision.
Businesses can configure the rules based on their definition of risk, making it easier for organizations to ensure that each employee follows accepted protocols, resulting in a safer work environment.
To see how Protex AI can help you prevent workplace hazards and ensure compliance, watch our demo.
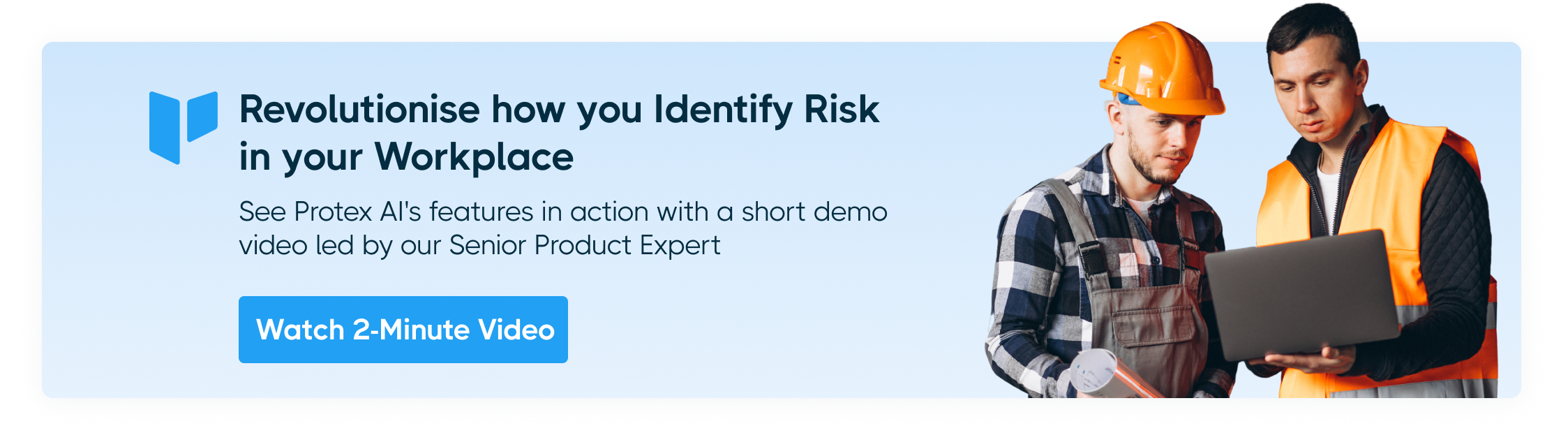