Safety Data Collection and Processing
What is Safety Data Collection and Processing?
The collection, storage, and processing of safety data is an integral part of any organization’s Environmental, Health, and Safety (EHS) program.
Having access to accurate and up-to-date safety data helps EHS managers identify areas for improvement in their organization’s processes.
Safety data collection and processing can help organizations ensure compliance with safety standards, and also mitigate the risks of workplace hazards.
It allows companies to take a data-driven approach to providing a safe environment for employees.
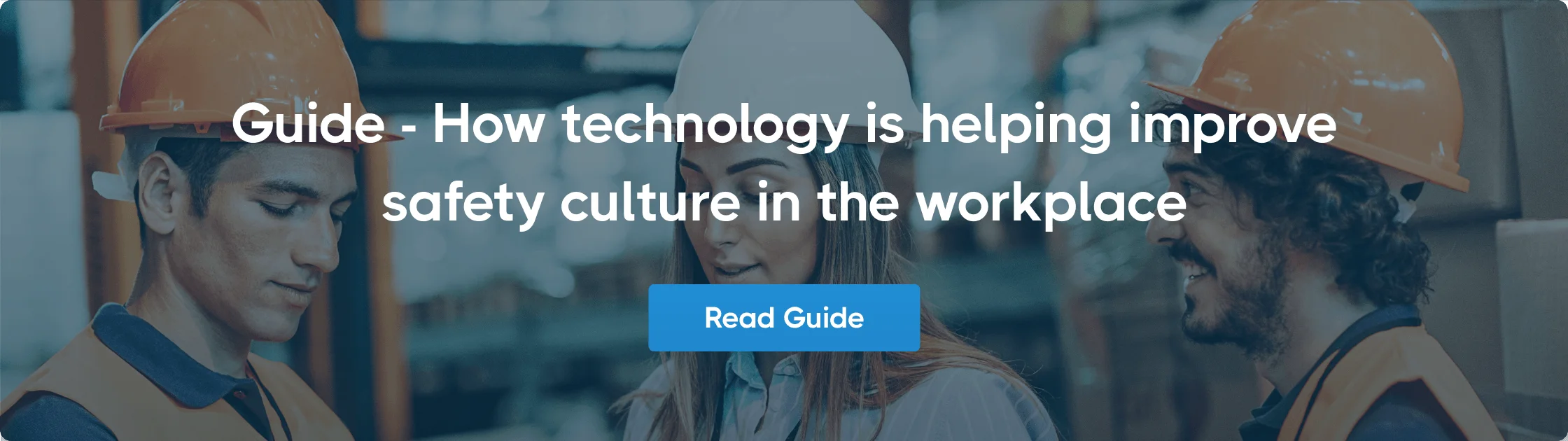
What is Safety Data?
Safety data helps identify workplace hazards and assess the risk those hazards pose to workers. This includes data on employee injuries, near misses, hazardous materials used in the workplace, industrial processes in use, and more.
The goal of collecting this type of data is to gain insight into the current state of safety in a workplace and develop strategies for improvement going forward.
Safety data provides a window into how safe your workplace really is. By analyzing this data, you can gain valuable insights into potential areas of risk that need to be addressed.
You can also track progress over time by comparing current results to past performance metrics - such as accident rates or frequency of near misses - which can provide valuable feedback on the efficacy of your safety initiatives.
Finally, having accurate records of safety incidents allows you to easily demonstrate compliance with local regulations or industry standards if needed.
The Importance of Safety Data Collection
Safety data allows you to measure, monitor, and analyze your organization’s safety performance. With a robust safety data collection system in place, you can gain insights into how your employees are interacting with their workplace environment on a daily basis.
For instance, if employees fail to wear PPE in a high-risk area, companies can review safety data to identify the reasons behind this. They can use this information to then ensure that employees do not leave themselves exposed in high-risk work environments.
How to Collect Safety Data
Here are a few steps that companies can take to collect safety data in the workplace.
- Create a Data Collection Plan
The key to effective safety data collection is having a well-organized plan in place. This plan should include specific goals and objectives, as well as detailed procedures for gathering, analyzing, and reporting on the data.
You should also consider who will be responsible for collecting the data and what resources they'll need to do it effectively.
It's important to review this plan regularly to ensure that it stays up-to-date and reflects any changes that have occurred in your workplace or industry.
- Identify Data Collection Processes
The most important data points to collect are those related to incidents and injuries. These include information on:
- The type of incident or injury (e.g., slips/trips/falls)
- When it occurred (date and time)
- Where it occurred
- Who was involved (name or job title)
- How it happened (describe the sequence of events leading up to the incident)
- What caused it (if known)
- What corrective action was taken (if applicable)
- Any resulting medical issues or lost time from work as a result of the incident.
Additionally, near miss reports should also be collected in order to identify potential hazards before they become actual incidents or injuries. When it comes to safety data collection, metrics are the most important.
The type of metrics you choose to track will depend on your organization’s specific needs, but some common ones include injury rates, accident reports, employee satisfaction surveys, equipment maintenance records, and training records.
It's important to not only collect these metrics but also analyze them so you can draw meaningful conclusions from the results.
- Establish Sources for Data Collection
It’s also important to identify the different sources through which safety data will be collected in the workplace. Companies can record data through various sources, including:
- Surveys
- Observation
- Checklists
- Incident reports
- General forms
- Interviews with employees or stakeholders
- Focus groups
Many companies now use AI-powered safety solutions to gather safety data. Advanced workplace monitoring solutions can be connected to existing CCTV networks, automatically identifying risky behavior and tracking hazards.
Data Analysis and Reporting
Once you have collected your safety data, it is important to analyze it in order to gain useful insights about potential risk areas within your organization.
This analysis should include identifying patterns or trends within the data set as well as any outliers that could indicate an issue with specific processes or operations that need attention. The analysis should also consider any external factors that could influence the results (e.g., industry trends).
Use Protex AI to Supercharge Your Safety Data Collection and Processing
Protex AI can give you access to actionable insights about your company’s safety performance. It can monitor safety events and automatically create logs, empowering EHS teams by giving them access to more actionable data about the company’s safety performance.
It automatically generates detailed safety reports and features flexible markdown to allow EHS teams to add their notes before sharing the reports with other shareholders. It’s a fantastic solution that companies can use to improve workplace safety standards.
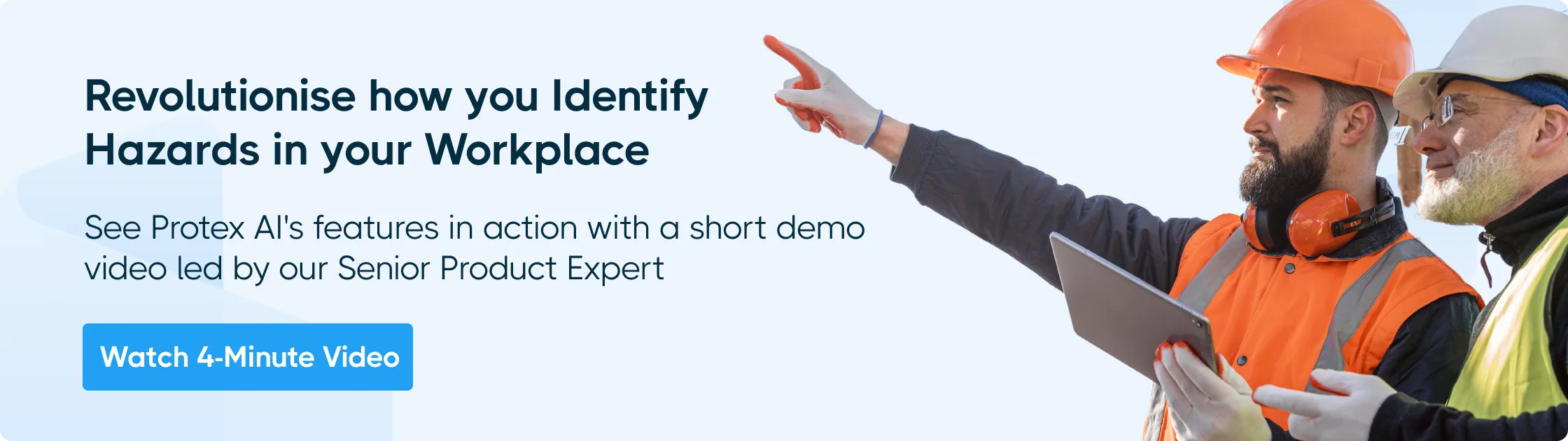