Manual Handling
What is Manual Handling?
Manual handling is a term used to describe the process of lifting, carrying, pushing, pulling, and moving objects by using physical force.
Although manual handling tasks are common in many workplaces, the risks associated with handling heavy objects should not be ignored. Injuries caused by manual handling activities can lead to serious health complications, reduced productivity, and increased costs for employers.
For this reason, every workplace must prioritize the safety and well-being of their workers by implementing effective manual handling techniques and procedures.
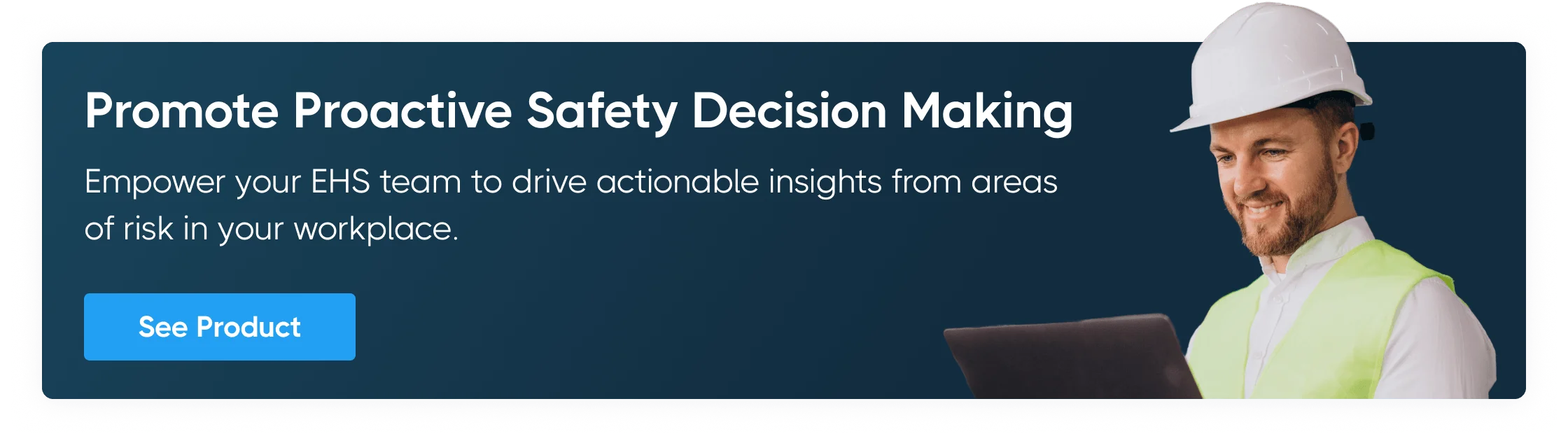
The Risks of Associated with Manual Handling
There are many risks associated with manual handling, such as:
Musculoskeletal Disorders
Manual handling involves moving heavy or bulky items by hand, which can cause injuries to muscles, ligaments, and tendons.
These injuries fall under the category of musculoskeletal disorders (MSDs), which can have long-term effects and continue to worsen if left untreated. They can significantly reduce a worker's ability to perform their job and can even result in permanent disabilities.
Employees who frequently engage in manual handling activities must take care to avoid excessive strain, repetitive motion, and awkward posture to reduce the risk of MSDs.
Slip, Trip, and Fall Injuries:
Slips, trips, and falls can also occur in manual handling tasks, leading to serious injuries. These hazards occur when workers fail to clean up spills, keep their work area organized, and wear proper footwear.
Proper training in preventing slip and trip hazards, as well as keeping walkways clear and unobstructed, can prevent these accidents.
Manual Handling while driving
It is not only inside the factory or warehouse that manual handling is required. Driving positions like delivery drivers, forklift drivers, and crane operators require manual handling.
In these instances, workers are vulnerable to accidents, including vehicle collisions and taking the brunt of falling load. In addition to wearing protective gear, drivers must take defensive driving classes to reduce the risk of work-related incidents.
Lack of Training
The importance of proper training cannot be emphasized enough when it comes to manual handling.
Employees who are not trained on proper manual handling techniques are at a higher risk of getting hurt on the job than those who are correctly trained. Workers must learn how to assess weight and proportions, how to utilise lifting equipment properly, and how to identify potential hazards in the workplace to reduce the risk of injury.
Poor Equipment and Work Practice
Many workplaces skimp on proper equipment and work practices, which increases the risk of injury. Workers must have access to equipment like pallet jacks, lifter, and dollies to transport heavy items safely.
Additionally, organisations must implement safe work practices like using proper lifting techniques, taking breaks, and rotating jobs that involve manual handling to reduce fatigue and minimise risk.
The Importance of Risk Assessments
Risk assessments play a critical role in identifying the risks associated with manual handling activities and developing strategies to mitigate them.
Every employer must conduct a thorough risk assessment of their manual handling tasks to identify the risks that may be posed to their workers.
Risk assessments should be based on the nature of the task, the objects to be handled, the distances to be carried, and the working environment.
Employers must also ensure that their workers receive appropriate training and guidance on the safe handling of objects, including the use of lifting equipment and techniques.
Employers must continually review their manual handling procedures and make appropriate adjustments to improve safety, productivity, and overall workplace well-being.
This may include investing in new equipment, providing additional training, improving working conditions, and revising risk assessment procedures.
Employers must also encourage workers to raise any concerns or suggestions related to manual handling tasks.
The Importance of Teamwork
Manual handling tasks should be carried out by teams rather than individuals. Working in teams reduces the risk of injuries and improves productivity.
The team should have clear communication channels to ensure that everyone works together safely and efficiently. Employers must also consider the physical abilities and limitations of their workers before assigning manual handling tasks.
Workers with pre-existing health conditions or disabilities may require additional support and adjustments to ensure that their manual handling tasks do not pose any risks to their health or well-being.
Protex Can Help Companies Reduce Manual Handling Injuries
Protex is a AI workplace safety solution that helps companies identify any unsafe events. It allows companies to create a positive culture of safety and makes it easy for companies to better understand how employees approach safe handling procedures.
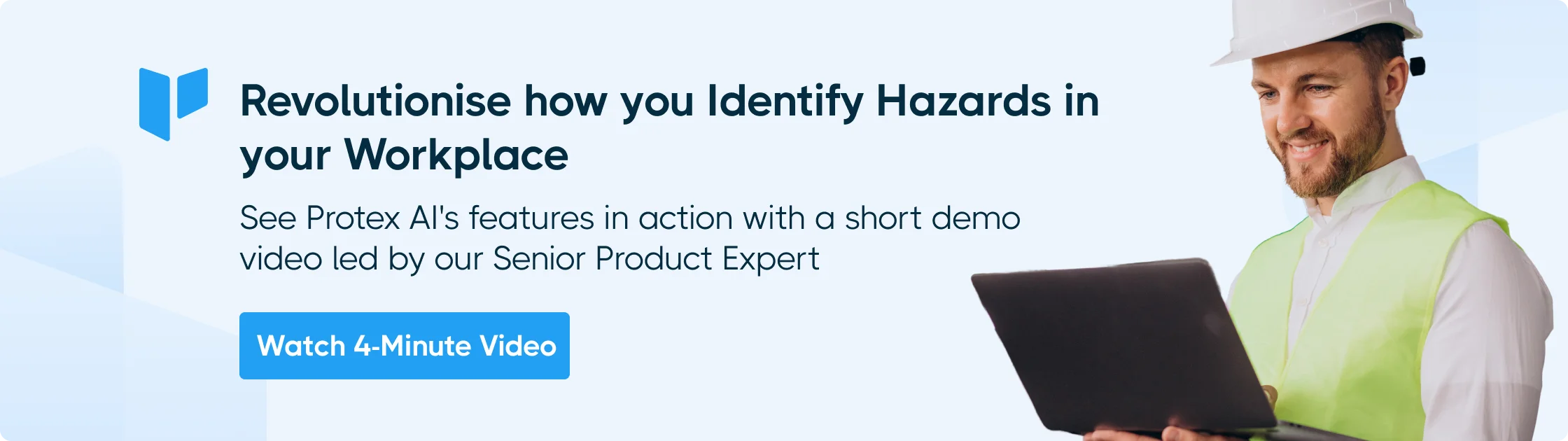