Hazard Analysis
What is a Hazard Analysis?
A hazard analysis is a thorough evaluation of hazards that may exist in a workplace. Hazards are defined as any situation or object that may potentially be a source of harm or result in damage to property.
In simple terms, anything or any circumstance that can result in an occupational safety issue is a hazard. Employers are responsible for conducting a thorough analysis in order to identify, mitigate, or eliminate all hazards in the workplace. To do this, they must conduct a hazard analysis.
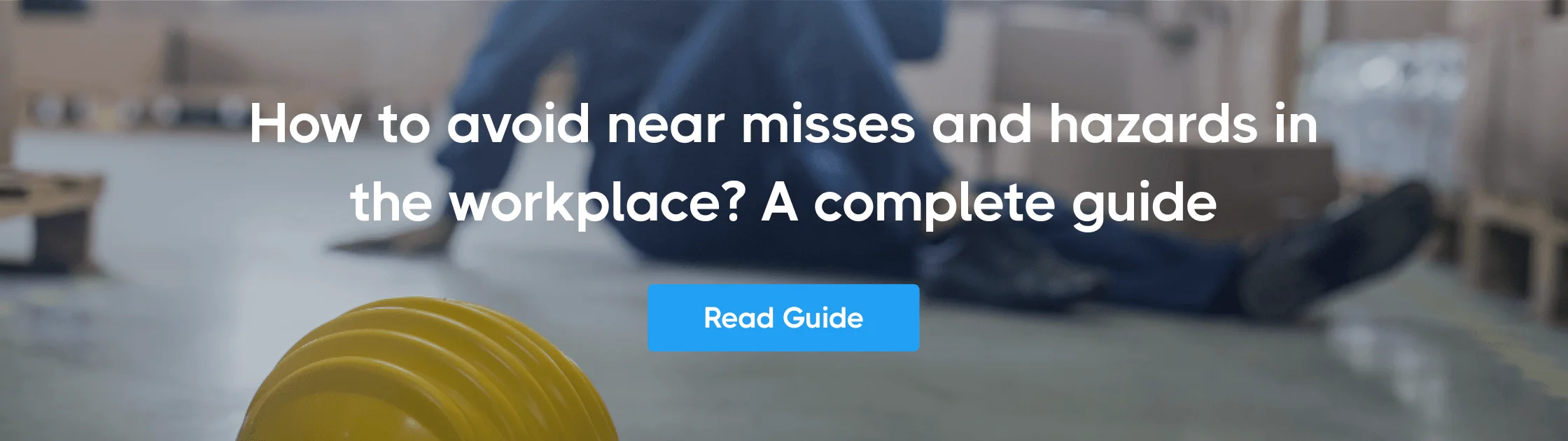
How To Conduct a Hazard Analysis
There are three main steps involved in conducting a hazard analysis: identification, evaluation, and defining controls to mitigate or eliminate them.
1. Identifying Hazards
The first step is for EHS teams to properly identify hazards in the workplace. In general, hazards in the workplace can be broadly categorized into different categories:
- Biological hazards
- Chemical hazards
- Physical hazards
A Process to Identify Workplace Hazards
The first step is for EHS teams to prepare a list of all the hazards that exist in the work environment.
This may require EHS teams to conduct interviews and leverage employee experience and knowledge, as well as review any document issues with production.
They will also have to rely on their knowledge and understanding of work processes to create a detailed list of all hazards.
This is an incredibly important step, and teams are required to be as methodical as possible so that they don’t overlook any step.
2. Evaluating the Risks
The next step is to evaluate the risks of these hazards. A risk is essentially the likelihood of that hazard occurring and the severity of damage it may cause.
Reviewing Existing Hazards and Controls
When evaluating the risks posed by hazards, EHS teams will want to look at existing procedures and controls and test their effectiveness. Furthermore, they may also rely on their experience and knowledge to better understand the risks.
Defining Severity and Potential Impact
A detailed report must be prepared to define the severity of hazards. This report should categorize hazards based on their potential to cause:
- No safety effect - Minimal or no impact on safety and health.
- Minor injuries or illnesses - Injuries that require attention but are not life-threatening.
- Serious injuries or environmental damage - Hazards that may result in significant harm, including workplace injuries or environmental harm.
- Catastrophic outcomes - Hazards deemed catastrophic could cause multiple fatalities or severe property damage.
Prioritizing Hazards Based on Likelihood
The report must also include the likelihood of these hazards, ranging from extremely improbable to highly likely. This helps companies in establishing the priority of which hazard to deal with first.
3. Devising Controls
Once the company has identified potential hazards, the next step is to devise control measures to mitigate or eliminate the risks that they pose.
This involves creating a report detailing the measures, including how they would help in hazard prevention and safety risk management. For instance, if there are specific tasks to be performed, the report must specify:
- The tasks
- The order in which they must be carried out
- The operating procedures
- The frequency
- Who is responsible for carrying out the tasks
Any evidence that shows how the measures can control a hazard must be included within the report, demonstrating their effectiveness in reducing the risk and ensuring compliance with process safety management guidelines.
Not all hazards can be fully eliminated. In some cases, companies only devise control measures, such as engineering controls or administrative controls, to bring these hazards within acceptable safety levels.
Educating and Training Employees
The final step involves educating and training employees about how to effectively mitigate these hazards. This is particularly important for managing hazardous chemicals and addressing possible failure modes that could lead to injuries and illnesses.
Employee commitment and collaboration are extremely important, without which it’s impossible for companies to create a safer work environment.
Companies must disseminate safety plans and provide comprehensive training to help employees recognize what is a hazard in the workplace, follow safe operating procedures, and use personal protective equipment as necessary.
Use Protex AI to Conduct a More Accurate Hazard Analysis
Protex AI is a workplace safety solution that uses artificial intelligence to help companies conduct a hazard analysis and gather video evidence of different hazards.
Once they have this data, EHS teams are in a better position to identify various hazards and create more effective plans for hazard control.
More importantly, Protex AI allows companies to track how their safety measures are performing, or if employees are complying with instructions.
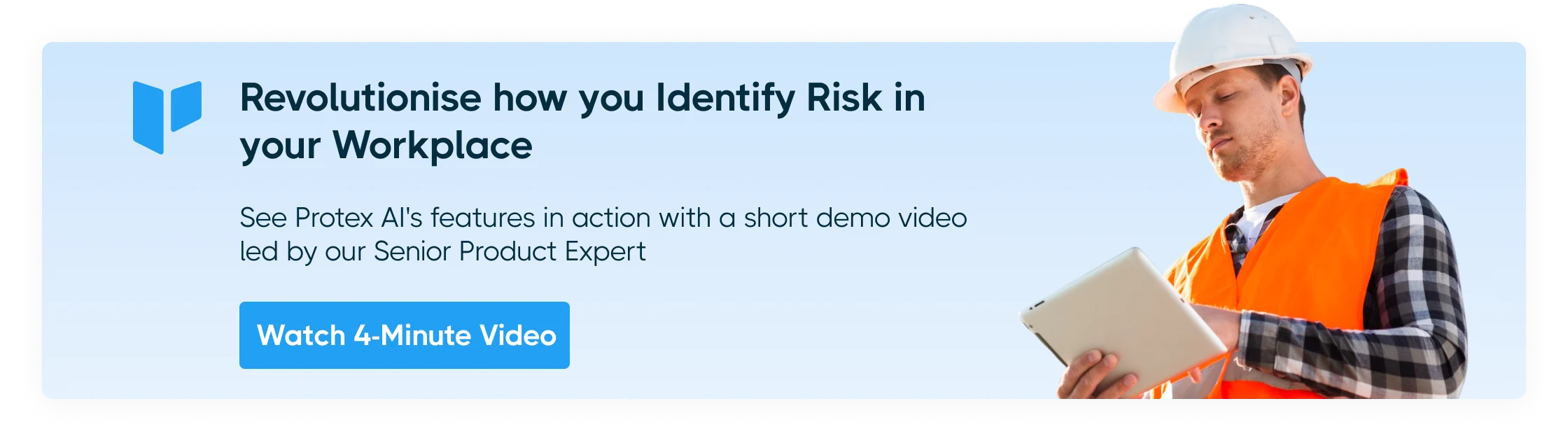