Accident Prevention
What is Accident Prevention?
Accident prevention refers to the strategies, preparatory methods, and the measures instituted to prevent accidents.
Accident prevention is an umbrella term that encompasses all steps taken for the prevention of accident occurrences, saving lives, and reducing injury severity.
It also includes steps taken to reduce property loss, bring down the costs of compensation or treatment of employees, and reduce the loss of morale and employee productivity.
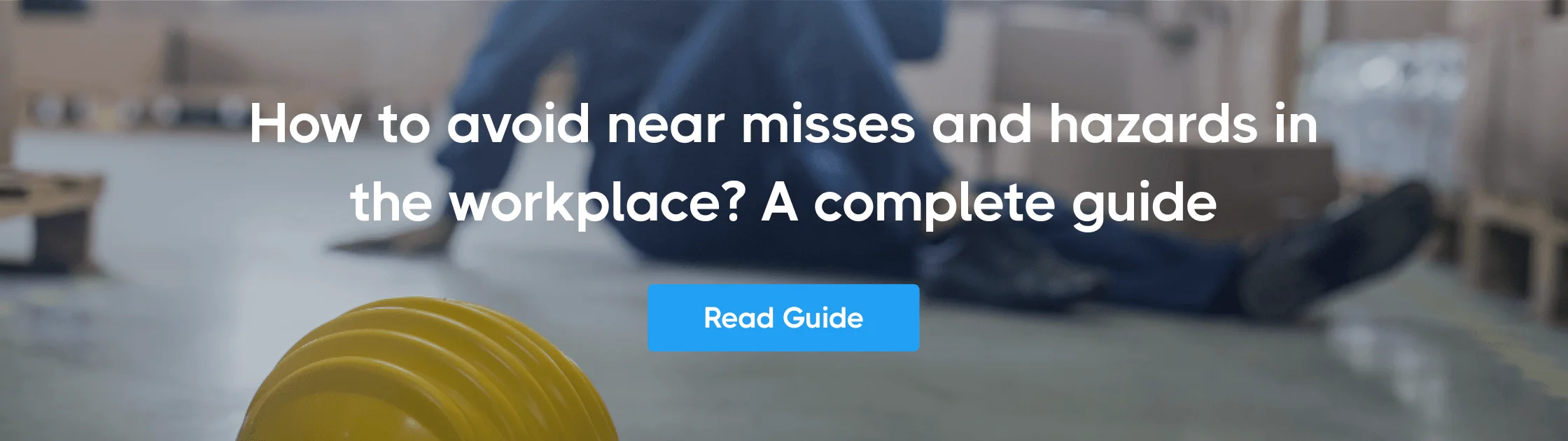
How Can Companies Prevent Accidents?
Accident prevention in the workplace primarily includes different procedures and policies instituted by an organization to ensure the safety of its employees. Any unexpected event that results in injury or property damage can be referred to as an accident.
Depending upon the nature of a company's business, workplace accident prevention plans may vary. Companies can reduce the risks of accidents by using different techniques, such as:
- Tailored Safety Training for Employees
Training employees to identify different hazards is fundamental to accident prevention. By empowering workers with the knowledge to recognize risks, companies can create a proactive safety culture. Incorporating behavioral safety principles is key to ensuring that these practices become ingrained in daily operations.
- Clear and Visible Signage
Posting appropriate accident prevention signs in critical areas can alert employees to potential dangers and guide them toward safe practices. Signs with standard color schemes, such as fluorescent colors for caution signs with white letters on a white background, ensure high visibility and remind employees of the safety program in place.
- Implementation of Robust Safety Policies
Instituting safety policies specific to the company's operations can significantly reduce risk. These policies serve as a framework for safe behavior and operational procedures.
- Diligent Safety Log Maintenance
Maintaining safety logs helps track incidents, which is crucial for understanding trends and preventing future accidents. These logs are essential tools for ongoing safety assessments and training. Thanks to these logs, companies can implement more targeted measures to reduce incidents in the workplace.
- Proactive Hazard Identification
Diligent hazard analysis in the workplace and creating a comprehensive accident prevention plan to mitigate or eliminate the risks they pose is a proactive step towards a safe work environment. Regular assessments using accident analysis techniques can help adapt safety plans to changing conditions.
- Regular Testing of Safety Equipment
Regularly test safety equipment to ensure it functions correctly and is reliable in an emergency. This testing can be the difference between a close call and actual injuries. Accident prevention tags on equipment can serve as a reminder to perform these checks, adhering to safety standards.
- Development of Emergency Action Plans
Create emergency action plans that are easy to understand and implement. These plans ensure a coordinated and efficient response to any incident.
.png)
What is the First Step in Accident Prevention?
Accidents in the workplace can lead to debilitating injuries, lost morale and productivity, and may even result in loss of life. Companies must take appropriate steps to prevent accidents, as it's always better to prevent one instead of fixing the damage later.
A systematic review of safety interventions for accident prevention by NCBI underscores the critical nature of these preventive measures and their impact on workplace safety.
Strategies for Reducing Workplace Accidents
While employers cannot prevent every single accident, significant reductions in accident occurrences can be achieved through careful planning for different hazards and implementing measures to mitigate the risks they pose.
Legal Responsibilities and Safety Compliance
Employers are legally obligated to comply with local regulations, which include establishing standard procedures to mitigate risk and enhance safety. This legal framework is designed to minimize accidents due to various factors.
Common Factors Leading to Workplace Accidents
Accidents usually occur due to several factors, including, but not limited to:
- Negligence.
- Lack of appropriate safety training.
- Disregard for safety protocols.
- Lack of proper knowledge.
- Not paying attention.
- Unsafe working conditions.
Company Responsibility and Collaborative Prevention
It is the company's responsibility to ensure that they make the workplace as safe as possible. Accidents can occur due to faulty machines, poor design practices, and unidentified occupational hazards.
If companies don't take appropriate measures to mitigate workplace hazards, accidents will continue. Accident prevention is often a collaborative effort between employers and employees and requires commitment from both parties.
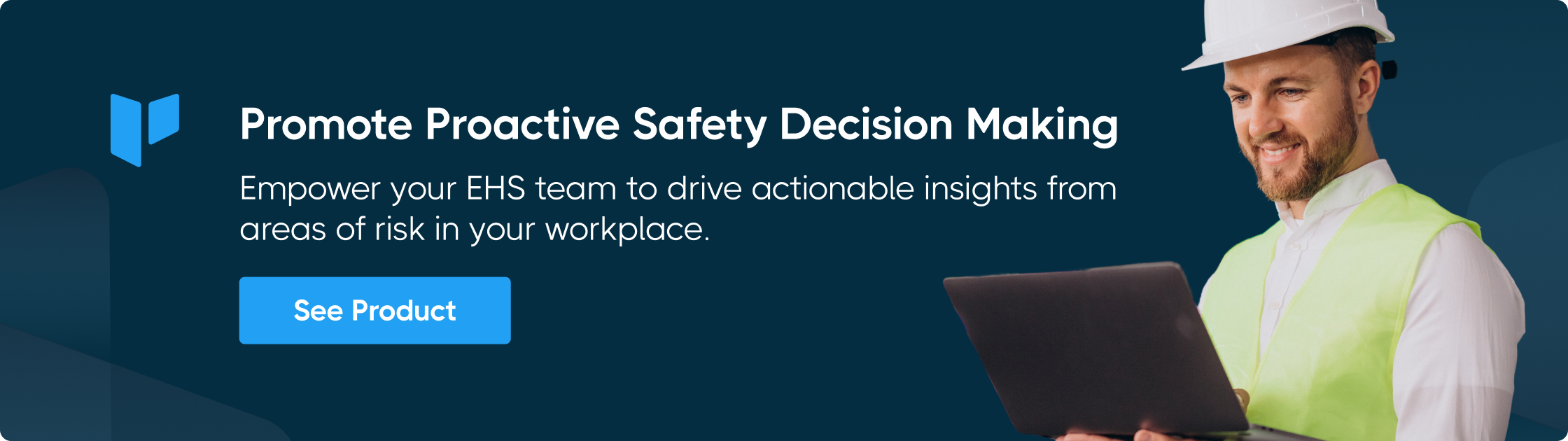
5 Tips for Effective Accident Prevention in the Workplace
Companies can significantly reduce the risk of workplace accidents by implementing various proactive measures.
These steps are not just about compliance with safety regulations but are integral to fostering a culture of safety and accident prevention.
By using risk detection and addressing identified risks head-on, businesses can create a safer environment for their employees and reduce the likelihood of accidents.
- Conduct Safety Inspections
One of the most effective ways to prevent accidents in the workplace is to conduct regular safety inspections. Safety inspections allow employers to identify hazards in the workplace and create actionable plans to mitigate or eliminate the risks they pose.
Because workplace hazards are constantly changing, companies must conduct inspections after regular intervals.
- Employee Safety Training
Companies must train and educate employees about hazards in the workplace and guide them about safe working practices.
Accident prevention courses, accident prevention policies, and accident prevention techniques are integral parts of this training, ensuring that employees stay safe, aware, and equipped to handle various occupational safety measures.
Training can be offered for different things, such as proper procedures for lifting heavy items, handling hazardous substances, and how to respond in case of an emergency. Employees must also be trained to operate machinery safely.
- Regular PPE Inspections
Personal protective equipment (PPE) is required for specific jobs. Companies need to offer protective equipment to employees performing risky jobs, ensuring that the PPE has a visible color seen even in the path of motor vehicle headlights or around vast machinery - for example.
Regular PPE detection using computer vision is another good example of an effective method in workplace accident prevention, ensuring that all employees are correctly equipped.
PPE such as helmets, goggles, and harnesses must be regularly tested to ensure they don't fail in case of an unexpected incident. These inspections are a key component of any comprehensive accident prevention plan. More importantly, employees must also receive regular training about how to use PPE properly.
- Using Appropriate Lighting
Making sure the workplace is adequately lit can also help in accident prevention, as good lighting is a design feature that supports occupational safety. It ensures that all areas are visible and can help establish and decrease workplace injuries.
For employees working offsite, the employer may have to arrange for proper lighting equipment as part of the overall workplace safety strategy.
- Imposing Limits on Manual Labor
Many jobs require employees to regularly lift heavy items and transport them from one place to another. Employers should impose limits on the number of trips each employee can make while also mandating regular breaks. Employers must also provide proper equipment and machinery to employees to reduce physical strain.
Prevent Workplace Accidents with Protex AI
Protex AI is a workplace safety solution that uses artificial intelligence to help companies reduce incidents in the workplace. The software connects directly to your company's existing CCTV network, capturing unsafe events, including near misses or safety breaches.
Our AI safety platform has been developed to meet industrial manufacturing safety requirements, allowing companies to make informed safety decisions and gain access to critical information that they can use when making decisions.
Protex AI also allows for better safety audits and automatically generates reports, showcasing the company's safety performance.
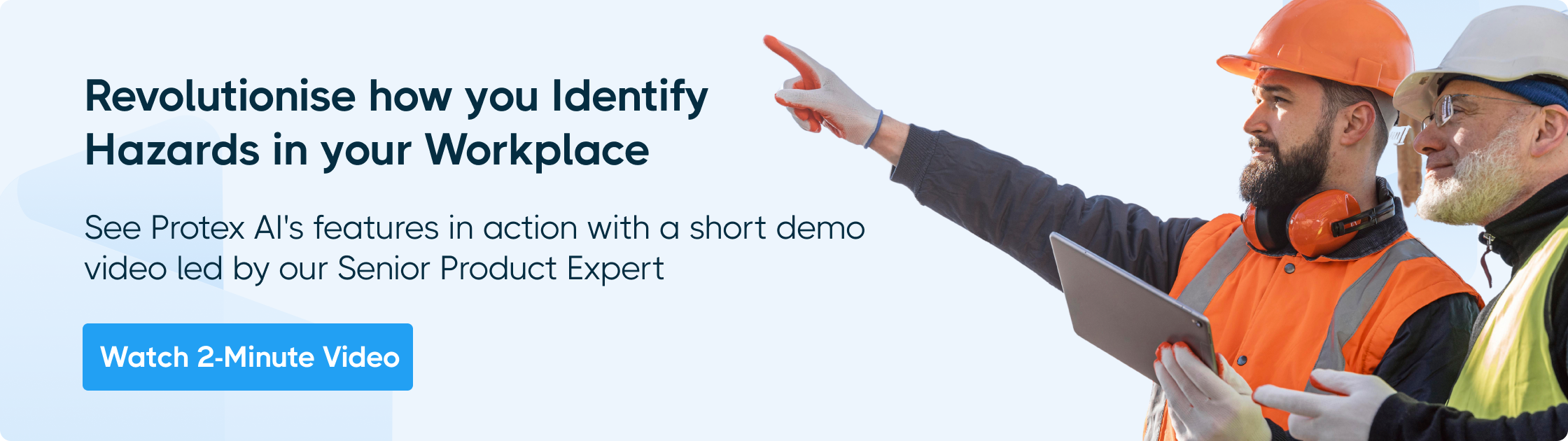